The Of Lone Star Supply Of Abilene
The 7-Second Trick For Lone Star Supply Of Abilene
Table of ContentsHow Lone Star Supply Of Abilene can Save You Time, Stress, and Money.Lone Star Supply Of Abilene Fundamentals ExplainedThe Basic Principles Of Lone Star Supply Of Abilene Getting The Lone Star Supply Of Abilene To WorkLone Star Supply Of Abilene Fundamentals ExplainedFascination About Lone Star Supply Of Abilene
Repairing these pipes often calls for additional repair work to satisfy existing building ordinance. Raised electrical problems that surge from poor electrical systems. The growing use of modern home appliances imposes a greater electric demand than these houses were designed for. The absence of outlets, outdated wiring and a limited number of fuses can make these residences hard to live in.The threat with lead paint depends on it ending up being air-borne when it begins to flake and break, whereupon professional aid is required for its elimination - https://www.ted.com/profiles/49599387. Asbestos, today recognized to pose extreme wellness dangers, was a popular building product from the 1940s to 1960s. Products like weatherboarding, pipes, cement and insulation often had asbestos
All About Lone Star Supply Of Abilene
Even with these problems, old houses from the 1940s possess an unique beauty with an appeal for those curious about reconstruction and restorations. Butcher Block Slabs abilene tx. Be sure to conduct a detailed examination of these homes before making an acquisition choice. Recognizing the attraction of these homes calls for an understanding of the wood house building methods used in the state of Wisconsin during the 1940s
Timber Frame Construction: Logs were changed by hand into flat faces and edges, organized using wood joinery, and covered with wood exterior siding. Timber Structure Building and construction: This approach counted on uniform, dimensional lumber from sawmills. The wooden structure was then positioned on a masonry structure. Allow's consider the preferred mounting strategies of that existing time: Balloon Framework: This was the best technique from the 1860s up until 1920 as a result of its simplicity.
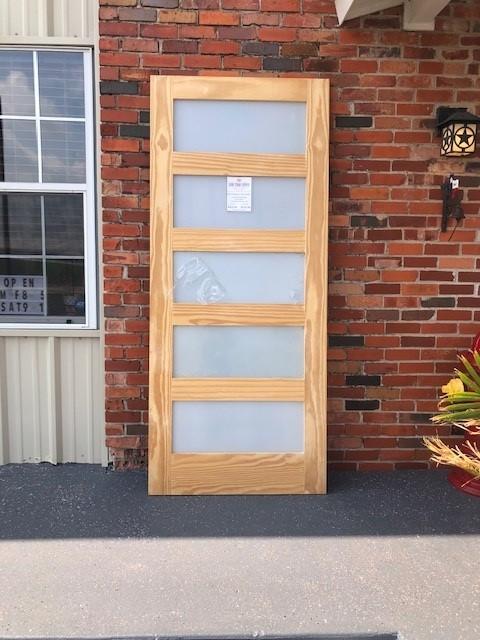
Rumored Buzz on Lone Star Supply Of Abilene
Historically, lumber utilized for building actually matched the small dimensions. For circumstances, a 2 x 4-inch stud was exactly that size. By the 1960s, this size had actually diminished to a finished measurement of 1-1/2 x 3-1/2 inches. Stonework building, another common method because age, experienced comparable availability and price modifications as a result of industrialization.
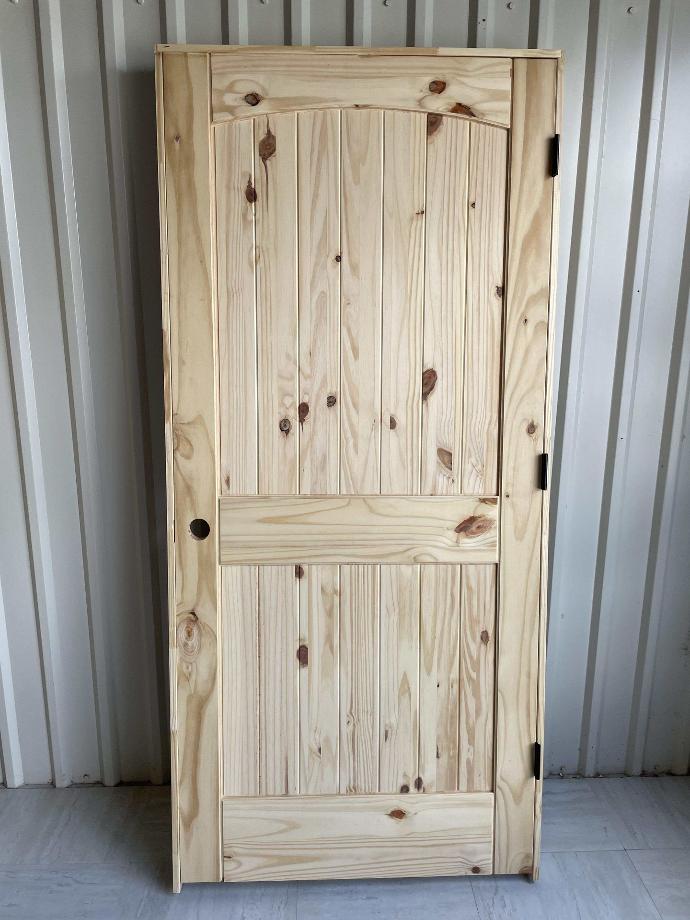
In between the 1930s and 1940s, cavity exterior wall surfaces on concrete strip foundations were presented, though roofs still did not have insulation. Hinged timber sash windows were fashionable. A lot of floor covering was elevated wood put on concrete strip structures, with shower rooms predominantly on the first stage. Message 1945, buildings had walls of non-traditional framework building and construction, with cladding of various products. building materials abilene tx.
A Biased View of Lone Star Supply Of Abilene
What products utilized in the 1940s to 1960s are currently known to be dangerous? Toxic lead paint and asbestos are known unsafe products utilized during that time. What were the typical approaches of timber home building and construction in Wisconsin in the 1940s? Three typical approaches were log building and construction, wood framework building, and wood framework construction.
Concrete, particularly strengthened concrete, is a reasonably new, yet dependable product in the construction sector. The addition of rebar inside the mix of concrete before it solidifies makes it stronger and longer-lasting.
The 7-Minute Rule for Lone Star Supply Of Abilene
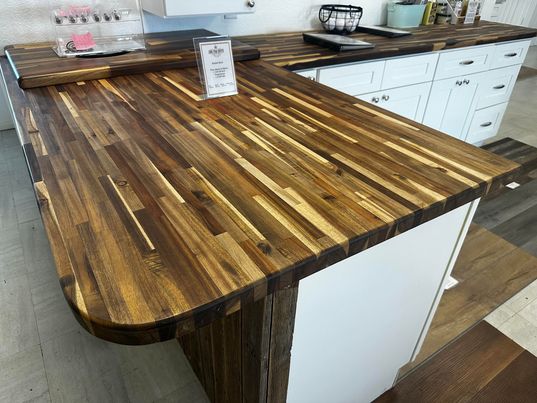
Higher-quality tiles typically have more prolonged guarantees. Metal roof covering: try to find materials like galvanised steel or aluminium which supply toughness and resistance to rust. Gauge the density of the metal as thicker gauges often tend to be extra resilient. Clay or concrete floor tiles: these are resilient and offer an unique visual.
Below are tests that individual home builders can execute without needing anyone's assistance: Knocking in floor tiles involves touching the surface area gently to examine its top quality. A clear, crisp noise shows a well-fired and structurally sound ceramic tile. Boring thuds or hollow noises recommend issues like air pockets or fractures. Aesthetically evaluate for any visible defects prior to installment.
Rumored Buzz on Lone Star Supply Of Abilene
If the water grains and stays externally, the timber is most likely well-sealed and shielded from moisture. If the water saturates right into the timber swiftly, it might indicate that it does not have correct sealing and might be vulnerable to rot or decay. Apply a strip of painter's tape firmly onto the repainted surface.
If the paint comes off with the tape, it recommends inadequate adhesion and might need sanding and priming before painting. Location a degree device on various components of the floor or surface area to look for evenness. If the bubble in the degree relaxes within the marked lines, the surface area is level.
Make use of a voltage tester to make certain electrical outlets are wired appropriately and securely. Inspect for proper grounding and polarity, and guarantee the outlets function correctly. Open and shut windows and doors to make certain smooth operation and correct placement. Try to find any sticking or dragging, which may show issues with installment or framework.